1111111
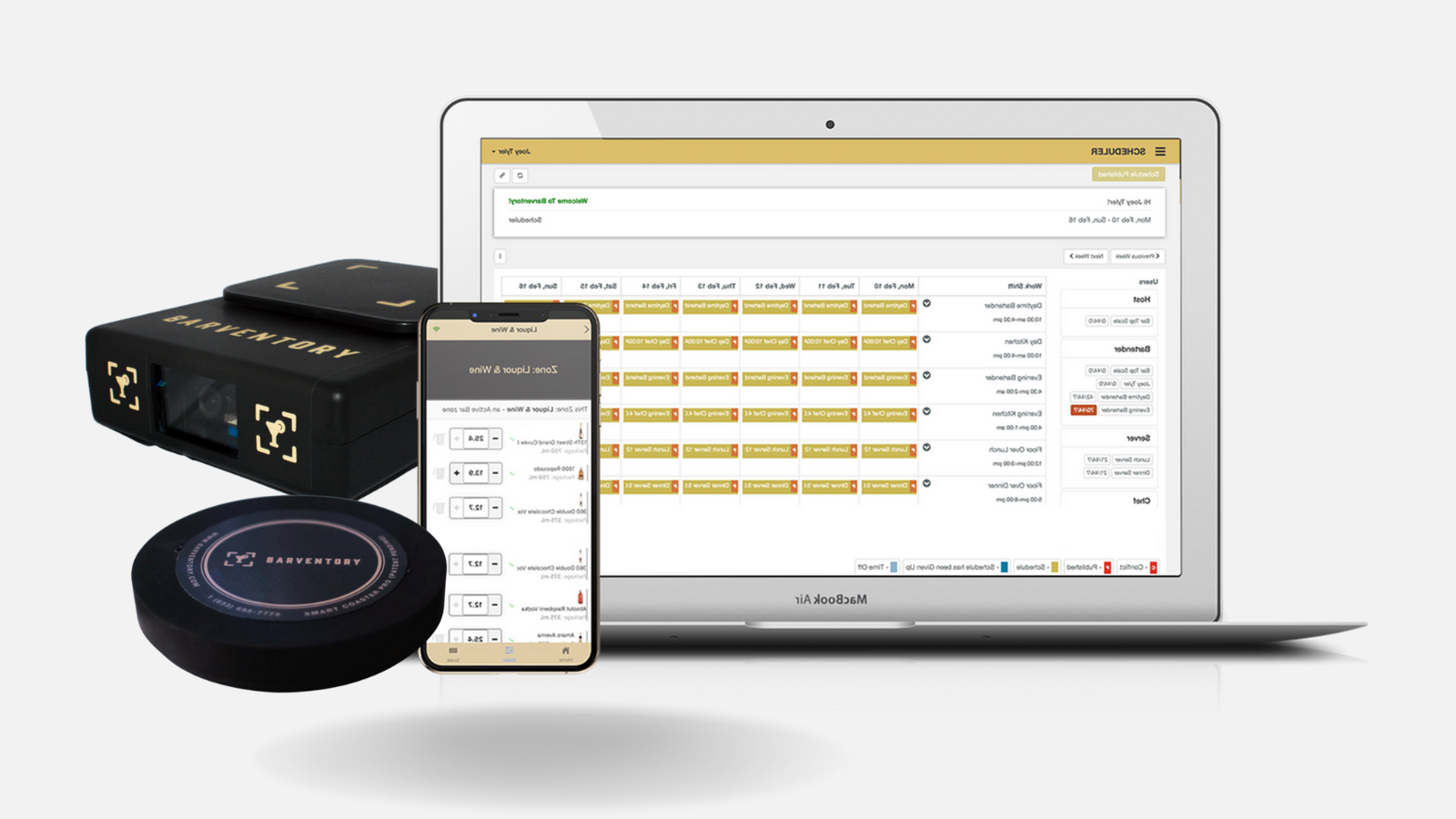
groupexadmin
August 13, 2024
0 Comments
Managing liquor inventory is one of the most crucial yet challenging aspects of running a successful bar, pub, or restaurant. Keeping track of every bottle, keg, and case can be overwhelming, especially if you’re using traditional inventory tracking methods, which mostly rely on manual data entry and paper-based systems. These old-school approaches can cause inaccurate counts and intentional overordering. However, real-time tracking systems reduce inaccuracies, resulting in significant cost savings.
The Costs of Inefficient Inventory ManagementPoor inventory management has several consequences. First, you can understock, damaging your reputation with your customers when you suddenly run out of a specific liquor. To avoid this problem, you might think that overstocking is the solution. However, ordering too much ties up your cash in stock, which might sit on the shelf for months. Other issues are overpouring, waste, and theft, adding to costs. These inefficiencies might seem small, but they can significantly increase your operating costs.
How Real-Time Tracking Solves These IssuesReal-time inventory tracking helps keep your liquor inventory records up-to-date on what is being used and what is left in stock. Automated reports also save time and reduce the risk of human error, giving you a clear and accurate picture of your inventory levels at any given time. Operators who have real-time access to inventory levels can quickly adjust their operations based on the demand.
As an operator looking to reduce operational costs, real-time inventory tracking reduces labor costs, storage costs, and waste due to overstocking and stockouts. This control over your inventory can significantly improve your bottom line.
Why Barventory is the Ideal SolutionWhen it comes to real-time tracking, Barventory understands the unique challenges of inventory management. That is why a team of bar owners and operators designed a system to weigh and track liquor inventory. This system is digital, more efficient, easy to use, enterprise-grade, and affordable compared to other methods.
Barventory offers a bar top scale with a built-in scanner that syncs to a digital app. The app has a built-in database containing thousands of barcodes of liquor products with photos of the bottles, so you don’t have to spend hours inputting your inventory.
How does it work?
1. Place the bottle on the scale and weigh it digitally down to the ounce using our proprietary algorithm to ensure accuracy depending on the type of liquor in the bottle.
2. Scan the bottle’s barcode; the app will identify it and display a photo from our catalog.
3. The liquor inventory is tracked in our robust, cloud-based inventory management system, which the bar manager can access in real-time from anywhere through a phone, tablet, or computer.
Additionally, Barventory offers a keg scale technology that monitors in real-time how much alcohol is left in your keg, accurate down to the ounce. This technology is particularly beneficial for beer kegs, where the ‘foam factor’ can lead to inaccuracies in traditional tracking methods. By measuring foam instead of liquid, traditional methods can leave valuable ounces of beer in your keg unaccounted for, increasing costs. This keg scale is accurate down to the ounce, doesn’t have a ‘foam’ problem, and provides a truly accurate way to know what’s in your kegs, helping you reduce waste and improve cost control.
These systems can be seamlessly integrated with other systems, such as POS systems, to provide a comprehensive overview of your entire inventory. This integration allows you to track your liquor inventory alongside other data points, providing a complete picture of your operations and enabling more informed decision-making.
Through a Groupex membership, you can access exclusive pricing and rebates for Barventory products.
Contact us today at 1-800-670-6800 or fill out this form to learn more about our programs.